Sustainable Innovations
Key Conversations: Consulting on Sustainable Production
When you meet Chandra Prakash for the first time and ask him ‘What do you do?’, he answers ‘sustainability consultant’ but it only takes one conversation with him to discover that in a moment he goes from working in the fields as an organic farmer to researching and developing sustainable agricultural methods in the production of natural fibers at the India-Nepal border and even more recently, securing the certification process of natural fibers using blockchain technology. Suddenly you realise ‘sustainability consultant’ doesn’t quite sum up the full scope, reach and vast nature of his work. In this interview we scratch the surface to reveal insights into his latest projects, challenges he is facing and his passion for true sustainability.

Can you tell us about your work as a sustainable fashion consultant?
I am deeply engaged with sustainable fashion and have gained invaluable insights on the its complicated supply chain from many perspectives; as an organic farmer, a textile designer, a fashion designer and as an entrepreneur selling textiles and fashion garments as the owner and founder of Cocccon specialising in the production of non-violent silk fashion. The creation and knowledge of short- and long-term sustainability road maps are my strength as a sustainability consultant.
You are currently researching other sustainable fibers and production methods, can you tell us what you are focused on?
My research is on natural fibers, in particular how they can be grown using as little water as possible and without chemicals. My current project aims to make the most sustainable and luxurious linen, kenaf & sisal fiber production located at the India-Nepal border.
You appeared in the Key Conversations video series with Simon Angel and introduced your latest technology solution to support the certification process for fabrics. Can you tell us more?
The challenges facing certification bodies have been further compromised by COVID-19. Most cotton fields are on isolated or rural terrain which means it is not possible to oversee or control the entire land. Data collection and entry is still based on trust, with no cross-verification methods. In the current system, it is not possible to authenticate the materials in the pre-fiber stages, such as the agricultural processes for growing fibers like cotton, linen etc. The lack of physical visits due to COVID-19 has resulted in the increase of greenwashing.
The technology I am currently developing can ensure auditing can be easy, safe and much more reliable. Data can also be collected at the agriculture stage. To ensure authentication, surveillance will be carried out at three different stages. Together, the use of AI technology, Blockchain technology and a smart physical auditing system will make the certification process of an organic product fool-proof.
Watch the Key Conversations episode between Chandra Prakash and Simon Angel here.
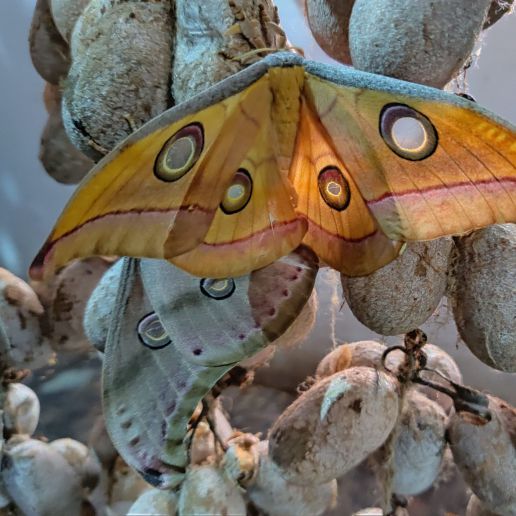

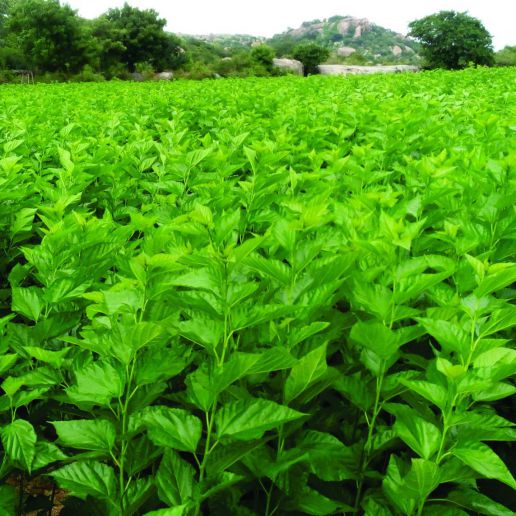
Tell us about the biggest challenge you face in the development of this new digital system?
This is very ambitious project. Traceability at raw material stage is supposed to be next to impossible. I took it as a challenge and worked hard on realising it. Connecting different kinds and levels of technology is always a challenge. Let’s just say we are working on it! We will need to work with partners from the fashion Industry including raw material and blockchain experts as well as crucial investors. We are currently looking for a CFO to join us as well.

How important is it for brands to offer transparency and traceability to their consumers? i.e adopting blockchain technology.
The number of people willing to buy authentic sustainable garments or fashion accessories has increased drastically. The young adults, teens and children who are protesting at Fridays for Future and climate strikes across the world are our future clients. They want to know who made the clothes they wear. They want to know if everyone was treated well in the supply chain. They want to know if their organic t-shirt is really an organic. Traceability will be the new normal soon. Our AI & machine learning technology can help everyone from brands to end consumers. Using Blockchain can ensure certifications are reliable and authentic.
Germany will introduce new Supply Chain laws with increased focus on human rights. Can your technology help avoid human right violations?
Current regulations have limited say and access to controlling social or human factors during the production stage of raw materials. There are also challenges in checking for forced or child laborer’s at cotton and flax-linen farming. 80% of cotton farmers working in developing nations are from local tribal communities and have no government approved ID cards. On paper, they do not exist, hence regulations are not applied to them. Our IoT based technology can help organise farmers and brands to overcome these challenges. This makes our technology suitable for fool-proof, real time traceability platform from farm to fashion.



Our thanks to Chandra for his insights and joining us in conversation as part of the Key Conversation series with Sustainable Innovations curator, Simon Angel. If you’re interested in the topics discussed here by Chandra Prakash or to find out how you can support his work you can contact him here: prakash@cocccon.de
Let’s keep the conversation going … did this project spark an idea or do you have any questions? We’d love to hear from you, send us an email to info@munichfabricstart.com
Key Conversations: Seamless Production with Mushroom Mycelium
Dutch designer Aniela Hoitink is on a mission to change the way we use textiles. Known as the living material, with MycoTEX Aniela harnesses the organic and living properties of the compostable mushroom roots. Showcased in our forum for Sustainable Innovations in 2018, MycoTEX® is the ground breaking automated seamless manufacturing method allowing for custom-made products made from compostable mushroom roots.
As is the nature of living things, change and progress is a constant. From the early beginnings until now, Aniela takes us on her journey and talks us through the evolution of this sustainable innovation. From founding her own company, NEFFA, to scaling up production of MycoTEX, here’s how Aniela is changing the future of textiles.

How has your work evolved since you exhibited at our innovation hub Keyhouse in 2018 as part of the Sustainable Innovations forum?
Based on feedback we received from brands and consumers, we have changed our growing method and successfully created samples which are smooth and can feature a variety of textures for unique placement options. Now further on, the first reactions from potential customers are very promising. We are working towards the development of a pilot collection over the next 12 months. Even more exciting, we have now established our company NEFFA. We have expanded our team and are raising a first funding round to produce the pilot production.
Have you seen a change in the way companies approach collaborations in the last few years?
The interest in sustainable materials has grown extensively. The goal is to find out how sincere this interest is. Do they really want to start working with your materials and products or are they just filling up their library?
What is the difference between MycoTEX and other (mycelium) materials?
Most companies are interested in developing sustainable materials that fit into the conventional supply chain, as this is the easiest way to make an impact. This conventional production method is based on cutting & sewing and overproduction. This way of production generates a lot of waste, waste that once needed water, nutrients and CO2. Our holistic approach led us to the development of an automated seamless manufacturing method for biomaterials. This allows us to make a bigger impact in terms of sustainability rather than using sustainable materials alone. As our method is not based on cutting & sewing, we do not have this production waste. Furthermore, our supply chain is much more flexible and allows for personalisation at mass production scale.


You are now in the process of scaling up the production of MycoTEX, can you share the highs & lows as well as the challenges you face to make this a reality?
Developing any company from scratch is hard but rewarding if you have a vision to follow. For us, the highs are all of the steps we take in the right direction. From finding the right partners who agree with your vision from the very first slide you show, to improving the material and achieving the result you like and more importantly seeing potential customers liking those results too.
The challenge is getting investors on board. A small ROI (return on investment) is something that most investors don’t like. The search to find the right investors takes a long time, trying to find those who are willing to join us and make an impact in the fashion industry. Clients are now used to sourcing sustainable materials and are approaching us for that reason. MycoTEX offers a product made using a seamless manufacturing technology which differs from the usual offer of fabrics by sheet or by meter. It can be challenging to convince them that our method is actually much more sustainable and worth the trouble to work with such an innovation.

MycoTEX was recently awarded the Solar Impulse Efficient Solution Label, can you tell us what this will do for MycoTEX?
To receive the “Solar Impulse Efficient Solution” Label, MycoTEX was thoroughly assessed by a pool of independent experts according to 5 criteria covering the three main topics of feasibility, environmental impact and profitability. It is an external validation of our solution, which helps in attracting customers and investors, as this is a proof of high standards in profitability and sustainability.


Who is your dream company to collaborate with and why?
We would like to work with innovative companies who are eager to rethink products being made, companies like Alexander McQueen, Martin Margiela or Mugler. Imaging the different shapes you can make if there is no need for seems, not even a shoulder or side seam. Kim Kardashian would be our dream type. Her curvy body is quite a challenge from a pattern-drawing point of view. With our seamless manufacturing method we could create the perfect fitting jacket for her.
Our thanks to Aniela for her insights and joining us in conversation as part of the Key Conversation series with Sustainable Innovations curator, Simon Angel. If you’re interested in a collaboration with Aniela Hoitink, she’d love to hear from you! Find out more here: https://neffa.nl/contact/
Let’s keep the conversation going … did this project spark an idea or do you have any questions? We’d love to hear from you, send us an email to info@munichfabricstart.com
Key Conversations: Natural dyeing as a future fundamental
Colour researcher Julia Kaleta is dedicated to strengthening colour communication and exploration into natural dyeing as a sustainable alternative for the fashion industry. What began as a passion project, the Atlas of Sustainable Colours now addresses a real need in the industry by providing comprehensive colour referencing and inspiration for natural dyeing.
Julia Kaleta sat down with Simon Angel as part of our Key Conversations video series to talks us through the evolutions or the work, the challenges of integration with design libraries as well as the realities embraced by sustainable fashion brands and designers making the move towards sustainable alternatives in dyeing.

Can you tell us how you work and the atlas itself has changed since you exhibited at Keyhouse in 2019?
During the exhibition I made a lot of new connections and shared a lot of inspiring conversations which made me ask myself more questions about sustainable colouring. Since then, the project changed a bit, but its main goal to be a catalyst and facilitate the debate on sustainable colouring in the textile industry has stayed the same. I am currently working on a digital platform for the Atlas of Sustainable Colours, nevertheless, it is a side project which I am developing in my free time so this is still in the development phase. I keep in touch with researchers and designers in the field to stay up-to-date with new possibilities and challenges of colour innovation. Recently, I applied for a grant to further develop my research but unfortunately didn’t secure the necessary funding which would speed up production of the Atlas of Sustainable Colours, to make it available for those who would benefit from having it in their design libraries.
What is the next step to this project?
The project itself sparks a lot of curiosity as people are very interested in what the project has to offer, usually following up with messages about how to get their hands on a copy. This shows that small brands and independent designers are in need for a guide into alternative colouring. My focus now is on production and realising my dream to make this book available to buy. In the meantime, I offer services as a sustainable colour consultant to help brands navigate the challenges of natural dyeing. While it is not the first catalogue of natural colours, the Atlas of Sustainable Colours is indeed the first compendium and comprehensive guide to colours made with alternative dyeing methods.



Tell us what you’re currently working on, is there something in particular which is new and challenging you have to tackle?
Last year was particularly challenging for me. Especially while undergoing work to realise the digital platform, it is much bigger project which is still looking for funding to take the project forward. I was invited as a guest lecture to speak with students on the topic ‘Ecological debate in fashion through the prism of colour’. It was an extremely fulfilling experience that has led to my decision to study for a PhD. From here I would say that the most challenging thing will be to remind myself to keep developing the project also way that is sustainable for me.
What’s your viewpoint on colour in fashion?
I look at colour as a tool to create an aesthetic experience. Therefore, I encourage every designer who is in the unique position of power to create new objects, to ask themselves not only about the origin of textiles but also to wonder where the colour comes from and how it was produced. It’s not always easy to find that information, but in the process, you will think more in depth about the complexity of the fashion industry and the importance of questioning the origin of the resources we use. These are the kinds of questions we must ask if we want to make more sustainable products and secure a sustaining life on this planet.
Do you have any advice to brands making the shift from synthetic to natural dyeing processes?
The best way is to open up a conversation with your textile supplier. In the end the goal is to recreate the fashion system, and if you are working with a textile supplier ask if they have in their offer colours made with natural ingredients. If they don’t have it, they will at least notice a demand for change. If your brand’s DNA focuses on optimizing waste and being more circular, it is great to look for fabrics dyed with waste from the food industry or embrace the process of making it on your own. It is important for a designer who wants to work with alternative colours needs to embrace the unpredictability of the outcome of the dyeing process. From a design side of things, it is important to consider the fact that natural colours may gradually fade away. Lastly, locality is a very important sustainable value. What does it mean in the context of dyeing? Look for local dyers in your country and start amazing collaborations with local studios who will dye your collection with indigo, madder or turmeric for example.
Who is your dream company to collaborate with and why?
Oh I would love the Atlas of Sustainable Colours to be in every design school both as a reference and inspiration. Besides that it would be amazing to collaborate with Natsay Audrey Chieza, one of the pioneers in bio-dyeing and a very inspiring woman, who works in a field of biotechnology and design.
Our thanks to Julia Kaleta for her insights and joining us in conversation as part of the Key Conversation series with Sustainable Innovations curator, Simon Angel. If you’re interested in a collaboration with Julia, she’d love to hear from you! Find out more here: https://juliakaleta.com/contact

Let’s keep the conversation going … did this project spark an idea or do you have any questions? We’d love to hear from you, send us an email to info@munichfabricstart.com
Sustainable Innovations presents Key Conversations
As the curator of the Sustainable Innovations Forum, Simon Angel keeps an ear close to the ground when it comes to the latest material developments and emerging design concepts. It’s no surprise then that from years of experience he is an expert in cultivating relationships and bridging conversations to strengthen connection and progress in the world of Sustainable Innovations. Don’t miss to read about last seasons’ developments presented physically in the Sustainable Innovations forum at MUNICH FABRIC START.

“I’ve always thought of the Sustainable Innovations Forum as a podium, the forum is a place where we can have conversations, discuss ideas and share information. It has become a place for connection and collaboration. In times when designers and sustainable innovators are isolated and we cannot meet as before, it is important that we do not lose this connection. “
Simon Angel, Curator of the Sustainable Innovations Forum
Together with Simon, we have initiated a new video series we are calling ‘Key Conversations’ as an extended platform of the Sustainable Innovations forum. Hoping to provide designers and innovators with the opportunity to prompt and exchange ideas.
Even though designers may feel a sense of disconnection as they work alone in their studios, there is still so much exciting progress being made. By inviting designers to join him in conversation, Simon hopes to resolve this paradox and once again create another platform for connection and facilitate an open exchange of unique insights and experiences.
What is Key Conversations?
Simon will invite designers and innovators from his network as well as past and present members of sustainable innovations community to join him in video conversation. We can look forward to the same lively and friendly interaction which is key to getting to the heart of the projects which Simon will bring on board here. Our goal is to offer tangible insights which can led to real life applications and collaborations by sharing these conversations with our online community.
What is the goal of these conversations?
Collaboration through conversation is key. By revealing insights and sharing an open dialogue there is an opportunity to connect and broaden the scope of what we believe is possible for designers and brands. We hope readers of this blog and viewers who watch our videos can connect with the projects on a deeper level and jump on the profiles and websites of the designers to learn more. There is always a chance to take part in the conversation by sending an email to Simon Angel or the designers featured.
What innovations will we hear about?
We are keen to provide our community with an update from our previous participates of the Sustainable Innovations Forum. Especially, we will hear about the progress and growth of their concepts since joining us at the Keyhouse. As well as this, Simon will speak with innovators in the fields of organic material development, natural dyeing solutions, and the use of natural resources in technology, among many more unique and diverse topics.
What now?
New videos and interviews will be shared on our social media channels and Munique Blog. We will feature upcoming articles here in an easy collection coming soon!
Let’s keep the conversation going … did this project spark an idea or do you have any questions? We’d love to hear from you, send us an email to info@munichfabricstart.com
A Look Back at 2020
It is popular to indulge in the mindset that we must put 2020 behind us and as quickly as possible. Ready to leave 2020 in the past and look only to the New Year for the future. As if there lays hope in 2021, like a magic wand it would undo and restart the world anew. But we must look back in order to look forward which is especially the case for creative innovator. In a year confronted with radical change, I can look back and break down general defining responses into three categories as:

Those who ‘endured’ change.
Those who ‘embraced’ change.
Those who ‘ignored’ change.
I think, as an allegory, this is what designers and developers ‘do’ every day. It is part of their daily practice: endure, challenge and ignore. From this perspective the majority of society is now familiar with the same practices designers have faced working in their studios’.
Looking back at 2020 among the broad network of designers and students, I am pleased to see that they have continued their practices. Perhaps you’ll be surprised to hear that a lot of them even made profit from the changes that Corona brought us. Designers from the sustainable front were celebrated. Shy geniuses were noticed and people who were previously unaware of the major flaws in the fashion and textile industry, could no longer ignore the cracks in the system: 2020 revealed the cracks and broadened awareness.
A positive response to change: the focus on sustainability and the sense of urgency to work in this way has never been clearer and has never before revealed the system ‘as a whole’ as clearly as it seems ‘NOW’. In previous articles, I pointed out that designers have a natural instinct to reflect on their contribution, to focus on their niche-solution but to observe the system as a whole. Discover the Sustainable Innovations series on the Munique Blog.
Now, however, the designers are no longer the front runners and exhausted messengers, screaming alone into the dessert. Instead, the industry: mills, dyers, production factories, governments and consumers seem to join forces and come together to solve the bigger problems in the system. This sense of urgency is a huge call for collaboration.
Meaning that our designers are free to take up a new position, leading innovation to new frontiers without the frustration of static movement from the industry. More and more, designers are re-thinkers and importantly, value collaborators. From this perspective I am very hopeful. We are still in a stage of responding to the established system, economy and behaviours … BUT I am very sure that the movement of change will continue to get stronger and broader than ever.
The challenge for now is to keep the focus on virtue, value and volume which has been the focus of our Sustainable Innovations forum since the January 2019 edition of Munich Fabric Start.
Virtue: having an idea about what you do, why you act and how this impacts society and our planet in a positive way
Value: the added value to the system, others and the whole as an effect on a certain act
Volume: think modest and act from need, not from greed

So, the actual risk in times of corona is to stress the choice between polarising OR collaborating; You are either ‘for’ or ‘against’. You are ‘in’ or ‘out’. The nuances, differences and challenges disappear from the stage. In the textile industry there is only one way: bridging the differences, uniting our similarities and cherish our authentic strengths, reminding me of the ‘Reach out and touch’ song.
The textile industry, as a front runner on fashion, can serve as the blueprint for a changing society and business practices. The ‘good’ practice. Connecting with the fact that all throughout history there exists no closer relationship to the human skin as textiles.

ABOUT THE AUTHOR
“I’m always keen to bring inspiring topics and sustainable projects into the spotlight through my work at the Sustainable Innovations forum at Munich Fabric Start and with each of my contributions to the Munique Blog. Check out @simonangelmfs for more sustainable projects, inspiration and discovery.“
Simon Angel | sa@simonangel.nl
From Trash to Treasure by Youyang Song
Dutchman Simon Angel has found a talented designer whose innovation makes it possible to create textiles from recycled bioplastics. The curator of SUSTAINABLE INNOVATIONS presented these and three other developments during the FABRIC DAYS.
„More and more, we are moving towards an era of adhocracy. Transferring this into the material and textile world: Materiality and comfort will experience a comeback”, explains Simon Angle in our interview with him.
An example of this is presented here as part of the SUSTAINABLE INNOVATIONS:
FROM TRASH TO TREASURE BY YOUYANG SONG
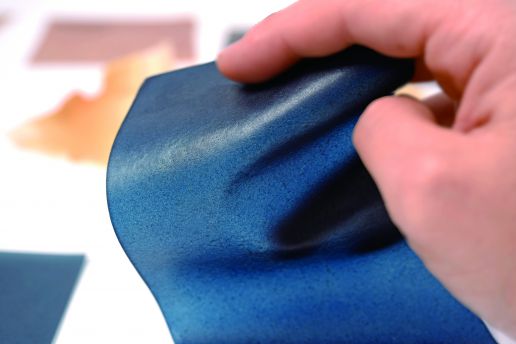
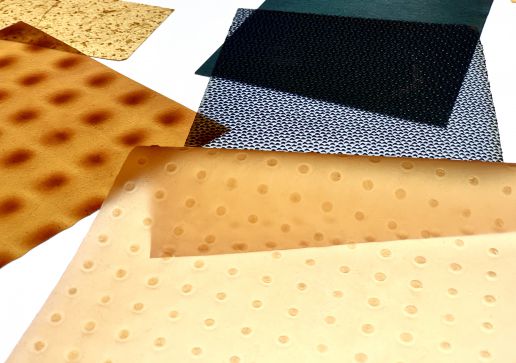

How can innovative products be created without using new resources? How can we stop growing mountains of waste? Use the old to create the new: The designer and materials researcher Youyang Song has set herself the goal of helping to develop an ecosystem consisting of purely biodegradable materials. Handbags made of banana peel, lampshades made of soy milk – the designer processes organic waste into new recyclable materials. This results in products that can be returned to the natural cycle at the end of the product life cycle.

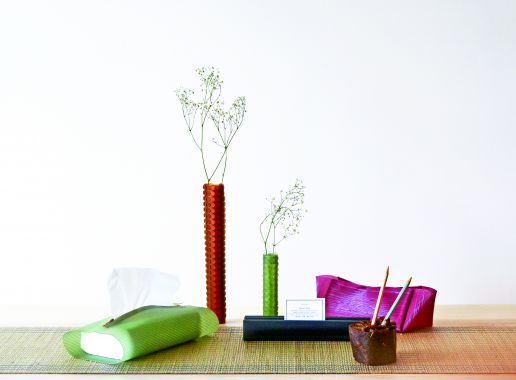
„Our goal is to establish a circular economy regarding the materials and follow the sustainable development guidelines to create our products.“
Youyang Song
Song has developed the “Cooking new materials” technique, in which fruit peels or soy milk are mixed with a natural binding agent. “APeel” is the name of the soft, innovative material created by this process. The natural product is also waterproof and robust like real leather, smells fruity, has a natural texture and is completely biodegradable. Protecting the environment in style: With her project, Song wants to show that environmentally friendly products can be not only practical, but also aesthetic and stylish.

Perfect Imperfection by Studio Mend
FABRIC DAYS presented futuristic innovations of international manufacturers. Besides, Sustainable Innovations curator Simon Angel introduced innovative developments of young designers in the SUSTAINABLE INNOVATIONS forum.
“Rethinking old traditions and adding a contemporary note to them can create innovation – sometimes you don’t have to come up with something entirely new to be innovative”, states Simon Angle in our interview with him.
An example of this “traditional innovation” is:
PERFECT IMPERFECTION BY STUDIO MEND
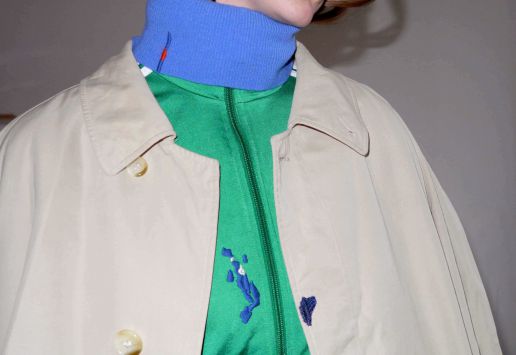
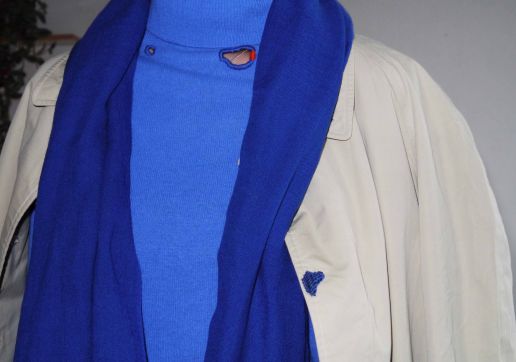
A new pair of jeans for 29,99€, a t-shirt for 7,99€. Constantly changing trends, synthetic fabrics and inferior quality: Since fast fashion conquered the world in the 1960’s, new clothes are available everywhere and at all times. What is broken is thrown away and what is no longer in fashion lies unused in the cupboard. More than two million tonnes of textile waste are generated annually in the European Union alone. When did our relationship to clothing change in such a way? This question was asked by the young fashion designer Sunniva Amber Flesland. She founded Studio Mend in 2019 to bring back the emotional and material value of what we wear.
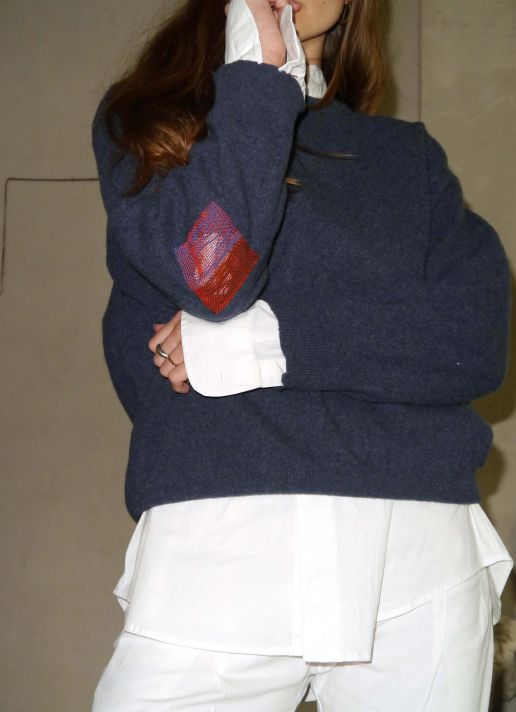
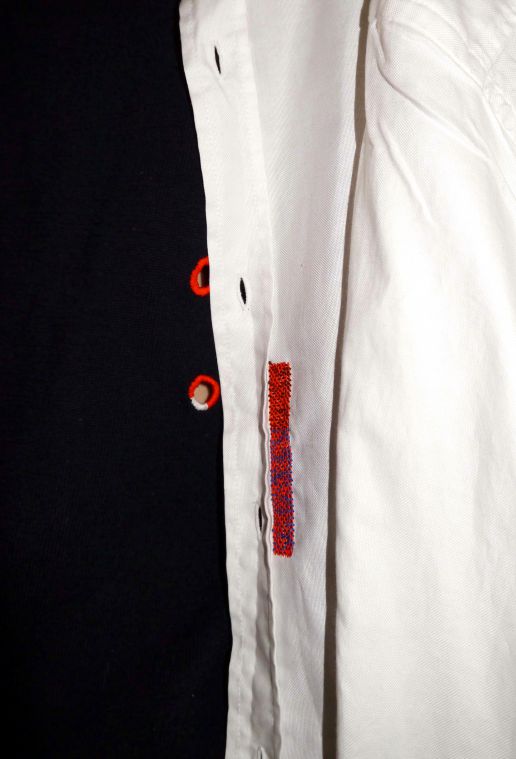
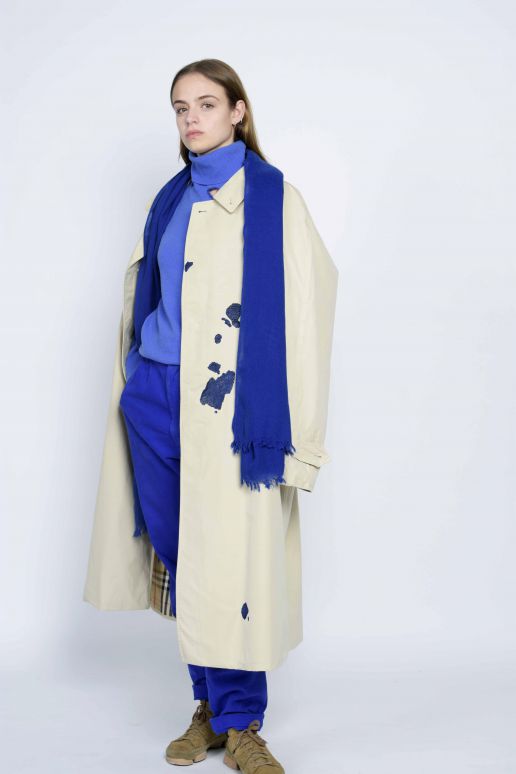
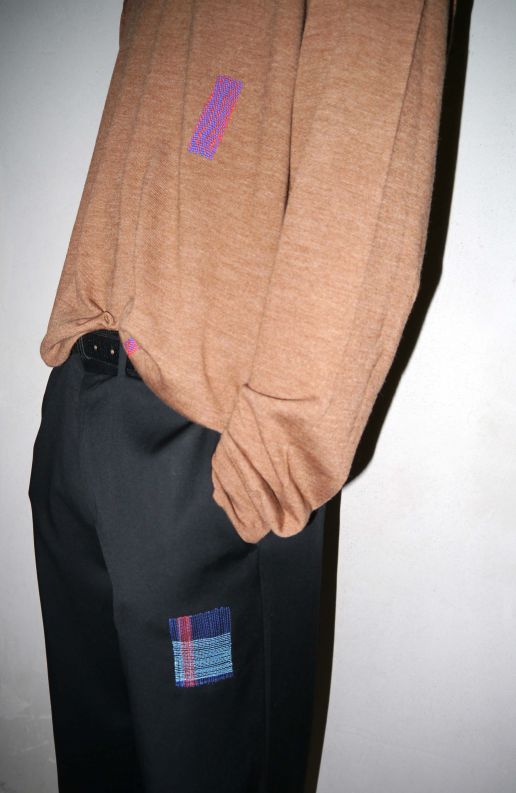
“I am excited by raw material, old crafts and traditions, beauty, and looking for potential where it’s not easily seen.”
Sunniva Amber Flesland
Appreciate, repair, refine: At Studio Mend, traces of wear and tear from through the lifespan of the garments are repaired in a very special way. Island Weave, Edge Mend, Pinstripe Patch, Crossover Stitch: The customer can choose between these four carefully developed technical styles to make his or her damaged favourite piece whole again. In combination with individual colour designs, valued and unique pieces are created. The acceptance of transience and imperfection – this is the basic principle of the Japanese philosophy Wabi Sabi, which served as inspiration for Flesland. Instead of hiding faults, they are celebrated as signs of an eventful life. Visibly and ingeniously, the artist creates valuable, aesthetic and unique pieces as a statement for a better fashion world.

Solar Self by Pauline van Dongen
SUSTAINABLE INNOVATIONS Autumn.Winter 21/22 #2
Every season, Simon Angel is searching for the four most futuristic SUSTAINABLE INNOVATIONS.
These four sustainable developments have been presented at FABRIC DAYS – one of them being this textile innovation that combines technology and fashion in a unique way:
SOLAR SELF by PAULINE VAN DONGEN


A dress to recharge your smartphone? What sounds like utopia is already tangible reality. For their project “Zonnestof” (“Sun Dust”), Pauline Van Dongen and Maaike Gottschal have developed a woven textile with thin, flexible solar cells, thus creating new aesthetic qualities and material properties. A play on colour, texture and transparency: By combining the solar cells with different yarns and various weaving patterns and techniques, a wide range of textiles can be produced.
“The creative process invites people to participate, to explore their dreams and wishes as well as to show what role solar energy can play in their daily lives. All participants become owners of the project through their contribution and thus part of a larger movement.”
Pauline van Dongen

But the Dutch fashion designers and researchers are not only interested in embedding technology in fashion. The initiators of the project are much more interested in the social experience of working with solar fabrics and wearing technology on the body. In workshops, the project invites the participants to create their own piece of “solar design” and weave a sustainable future. Instead of seeing nature and technology as opponents, Van Dongen and Gottschal want to make technology something that goes without saying. And it is not only fashion that can gain unprecedented added value from solar fabric: The textile can also be used in architecture or interior design, for new transport concepts and in public spaces as well as for events and festivals.


Living Material by Iris Bekkers
SUSTAINABLE INNOVATION Autumn.Winter 21/22 #1
SUSTAINABLE INNOVATIONS curator Simon Angel presented four developments for the season Autumn.Winter 21/22 at FABRIC DAYS at the beginning of September. The Dutchman is always on the search for interesting young designers, outstanding innovations and the latest novelties in the textile world.
In our latest interview with him, he stated: “With the Sustainable Innovation forum, we present the near future and showcase what already is possible.”
Let us now present you the first of this season’s SUSTAINABLE DEVELOPMENTS:
LIVING MATERIAL BY IRIS BEKKERS

Doesn’t fit anymore, doesn’t fit properly: Many of our favourite pieces of clothing lose their shape after a short time and are shipped directly to the nearest garbage dump. Textiles that adapt to individual body shapes and external conditions could reform the fashion and textile industry.
To create such textiles, product designer Iris Bekkers uses auxetic materials in her project “Moving Structures”, i.e. stretchable materials that can adapt their structure to their surroundings. As part of her final project at Eindhoven University of Technology, she has developed a special face mask that not only adapts to different face shapes, but also adapts its filter function to the environment and is very breathable.




More comfort, longer wearing time, less waste: Due to their geometric structures, auxetic materials become thicker when stretched, rather than thinner like most fabrics. The potential of such fabrics ranges from jackets that adapt to the seasons and can therefore be worn in summer and winter, to shoes that change their flexibility and stability as required. Bringing the material to life: For her designs, Iris Bekkers not only thinks about the material and its texture, but also about the context in which the fabrics are used and enjoyed. Only in this way can her designs combine man and nature.
“The auxetic samples are the start and inspiration for a range of products that can adapt and transform themselves, functioning optimally in different circumstances. The potential for adaptability results in more value, more function and a reduction in the quantity of materials and products necessary.”
Iris Bekkers



SUSTAINABLE INNOVATIONS, Big Changes & New Challenges
An interview with SUSTAINABLE INNOVATIONS curator Simon Angel – the Dutchman who is always on the search for interesting young designers, outstanding innovations and the latest novelties in the textile world. You will find Simon and the four SUSTAINABLE INNOVATIONS he chose this season in the foyer of hall 4 at FABRIC DAYS.
- Simon, what new innovations can we expect this season?
Rethinking old traditions and adding a contemporary note to them can create innovation – sometimes you don’t have to come up with something entirely new to be innovative. This edition ‘the new thing’ is referring to something old like weaving, repairing and recycling. For example, weaving with solar-panels from Pauline van Dongen, repairing as value-creation from Studio Mend or value adding applications by Auxetics and industry ready, recycled bioplastic fabrics by Studio YouYang. All these projects use traditional crafts and materials, but in a new and innovative way.
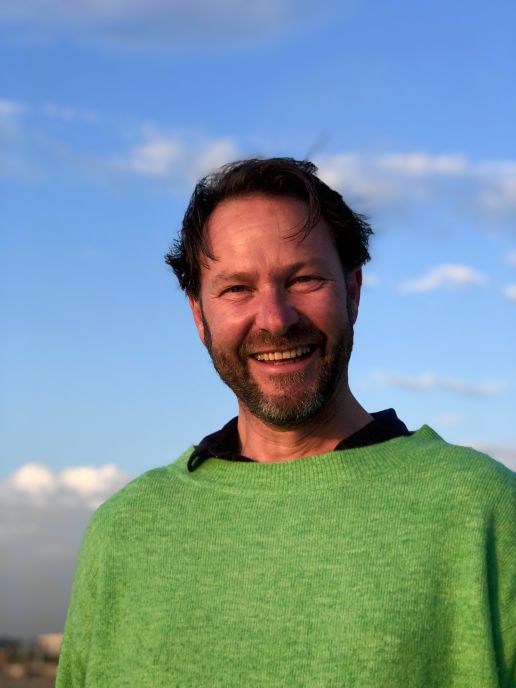
2. In 2020, the Corona pandemic brought the world to an unscheduled stop. But the crisis has also sped up the movement towards a more sustainable lifestyle. How will this shape innovation?
As you know, I’m an optimist. This year’s developments actually encouraged change. How you look at things makes a big difference in order to get yourself in the right inspired mode. Pandemics or heatwaves are nature’s way of confronting us. Just like we are experiencing changes in our environment, the nature experienced changed by humans for years and is now responding to us. All this is leading us to a dialogue with nature – a much needed one. Bit by bit we realise we exist as part of nature. Designers, scientists, the industry and consumers change their habits and question old methods. Finally, most of us start to realise what is necessary to ultimately save our world. We can only achieve that, when we are searching to find the balance with ourselves and with nature.

- It is the sixth time that you are curating the SUSTAINABLE INNOVATIONS. How has this year’s edition been different?
The responses to sustainable innovations are new. The dialogue is getting serious. For example, have a look at the location of the Sustainable Innovations forum this year: It has moved from the Keyhouse to the main hall, right in the heart of the industry. Right at the spot where the big changes happen.
- This year’s innovations are all about the material: textiles created out of biowaste fabrics, adapting its shape to the environment – can you give us a glimpse into the material of the future?
With the Sustainable Innovation forum, we present the near future and showcase what already is possible. As you can see, this future finds its inspiration in old traditions, crafts and resources. But what comes after that? It is hard to predict as the world is losing its linearity as we know it. More and more, we are moving towards an era of adhocracy. Transferring this into the material and textile world: design and shapes will not be the main focus of designers anymore. Materiality and comfort will experience a comeback – and we will have to redefine the product development process and all that entails. We have to open our minds and let go of expectations. We have to source from our universal knowledge to create something that in this form has never been there before.
- How can we see the current situation as an opportunity to innovate, rather than for all the challenges it presents?
This situation shows on a holistic level, that humans have to develop themselves and challenge the Status quo. Enjoy the experience as it opens up new horizons which we could never have dreamt of. Look at the Munich Fabric Start, with the Fabric Days they showed how to deal with unforeseen obstacles and ever changing circumstances – a pretty good demonstration of a future recipe for attitude, mental shift and permanent dialogue. So yes, let’s see every day as a chance for a better tomorrow.
Learn more about Simon’s sustainable novelties for the season Autumn.Winter 21/22 during the three days of FABRIC DAYS from 1 – 3 September 2020 at MOC Munich.
FABRIC DAYS AUTUMN.WINTER 21/22
OPENING HOURS
1 SEPTEMBER 2020 · 9.30 AM – 6.30 PM
2 SEPTEMBER 2020 · 9.30 AM – 6.30 PM
3 SEPTEMBER 2020 · 9.30 AM – 4.00 PM
LOCATION
MOC Munich | Halls 1 – 4 Ground Floor
Lilienthalallee 40
D – 80939 Munich